Cleaning the Vehicle:
The first step in the process is thoroughly cleaning the vehicle to remove any dirt, grime, leftover residue, or wax. This is a crucial step because any debris left on the surface can cause bubbles or imperfections in the wrap when laying it on the corners or edges of the vehicle. To battle this, we utilize a solvent-based cleaner or isopropyl alcohol to ensure that all residues are removed. Pay special attention to edges, seams, and recessed areas.
Inspection:
After cleaning, inspect the vehicle for any damages such as scratches, dents, or rust. These imperfections can affect the adhesion of the wrap and the overall final appearance. If there are any damages, they should be repaired before the wrap is applied, rather than laying vinyl over it. If not fixed, the spot in question will show up as a crease or bubble due to the uneven surface underneath.
Measuring the Vehicle:
Accurate measurements of the vehicle are essential as well. This includes all surfaces that will be wrapped, such as doors, bumpers, and fenders. This creates an opportunity to plan better and cut material for later use. Measurements should include curves and recesses to ensure that the wrap will adhere perfectly.
Creating the Design:
The design process involves creating graphics that fit the exact dimensions of the vehicle. The design should consider the vehicle’s contours and any features that might interfere with the wrap.And lastly, thanks to our in-house design team at SigmaGrafix, your brand’s ideas and must-haves are the ultimate goal we intend to achieve with your project! Your brand’s wants or must-haves, are easily and readily designable thanks to our superstar team we have allowed for one-off branded designs.
Printing the Wrap:
Once the design is finalized, and checked by our customers, it is printed onto vinyl wrap material. High-quality vinyl and inks are essential for durability and vibrant colors and being that we have them at our shops, it makes for a much more fluid process. Large format printers are typically used for this process to ensure seamless application on large surfaces.
Laminating:
After printing, the wrap is laminated to protect the graphics from UV rays, scratches, and weather elements. This step enhances the longevity of the wrap. Application is simple yet tricky, we have a team specific for printing and laminating making our company run much smoother and overall smarter!
Temperature and Environment:
The vehicle wrap should be applied in a controlled environment with a temperature between 60-80°F (15-27°C). This helps the adhesive work effectively and not become tough and agitating to use. A clean, dust-free indoor area is ideal and something we pay A LOT of attention to in order to prevent any particles from getting trapped under the wrap or adhering to anything during the process.
Positioning the Wrap:
Begin by positioning the wrap on the vehicle without removing the backing paper. This allows for adjustments to ensure the wrap is aligned correctly. We then utilize soft magnets or other hands to hold the wrap in place temporarily making sure our graphics line up with the correct contour lines.
Applying the Wrap:
Start from one section of the vehicle and gradually remove the backing paper as you apply the wrap. This method helps avoid large bubbles and misalignment. Use a squeegee to press the wrap onto the vehicle, working from the center outwards to remove air bubbles and ensure smooth application. Using an 80-50 degree angle allows for bubbles to be pushed out rather than utilizing force rendering the vinyl useless. For curved surfaces and recesses, use a heat gun to gently warm the vinyl, making it more pliable. This allows it to conform to the contours of the vehicle better and overall ease the stretching process.
Trimming and Tucking:
Once the wrap is applied, trim any excess material using a sharp blade(Exacto Knife). Be careful not to cut into the vehicle’s paint as it is right under the vinyl! Tuck the edges of the wrap underseals and around corners to ensure a clean finish and heat to adhere. This step prevents peeling and gives the wrap a professionally done look.
Post-Application Care/Tips
Post-Heating:
After the wrap is fully applied, use a heat gun to go over stretched or possible “loose” corners to make sure your wrap adheres well to the surface. This process, known as post-heating, helps set the adhesive and ensures a secure bond if it’s either cold, or you want to triple-check that your job is well done.
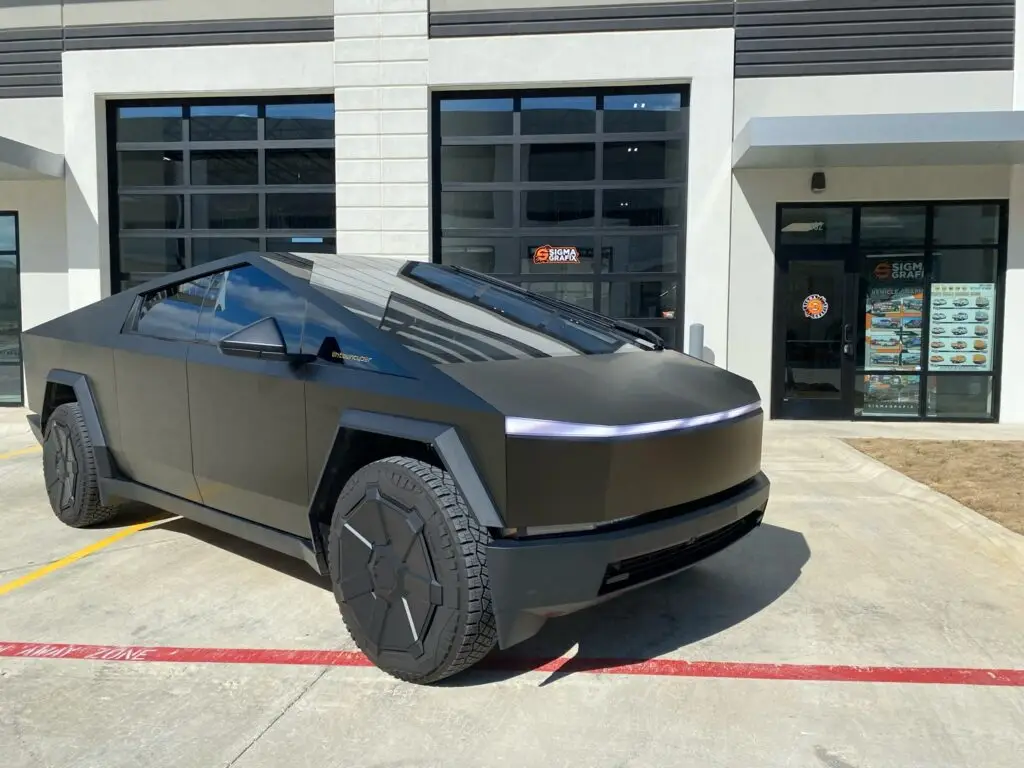
Inspection:
Inspect the wrap for any remaining bubbles or imperfections. Small bubbles can be removed by puncturing with a pin and pressing out the air with a squeegee. And lastly ensure that all edges are firmly adhered and there are no loose areas.
Curing Time:
Allow the wrap to cure for about 24 hours before exposing it to harsh conditions like car washes or extreme temperatures. This time allows the adhesive to fully bond with the vehicle’s surface. As a paint job or anything else, let it rest, then beat it up!
Cleaning:
Regular cleaning of the wrapped vehicle is essential to maintain its appearance. Use mild detergent and water, and avoid abrasive cleaning tools that can scratch the vinyl. Bird droppings and other chemical residues CAN and Will affect your wrap, clean it before they become one! Pressure washing should be done with caution, keeping the nozzle at least 12 inches away from the wrap and avoiding high pressure on the edges or corners, more prone to tear away.
Conclusion
Applying a vehicle wrap is an intricate process that requires attention to detail, the right tools, and a controlled environment. When done correctly, a wrap can transform the appearance of a vehicle, turning it into a mobile advertisement or a personalized piece of art. Working for some time in Dallas being ranked the “Best car-wraps in Dallas” we wanted to go south! With our new location providing truck decals and wraps in Spring, we hope to make a lasting impact on not only those in our customer base but also on creating a new place to call home for years to come. Call or email us today for the best auto wraps in Houston!